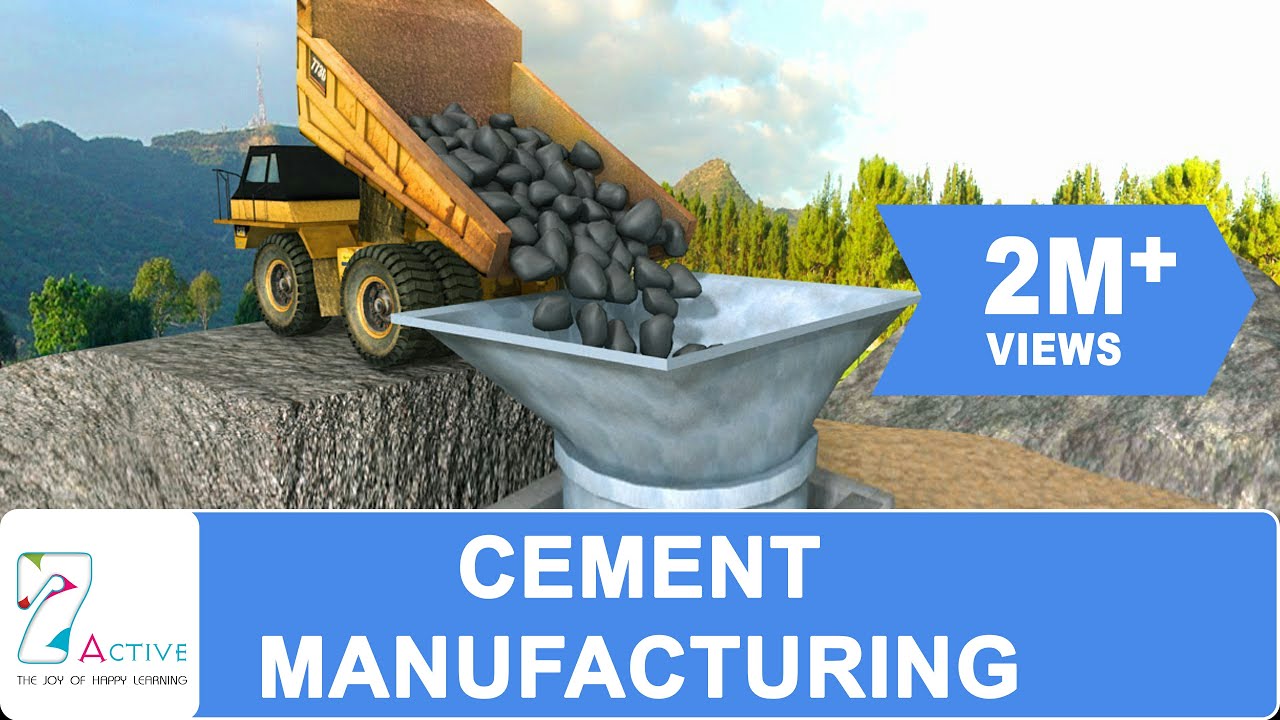
For more information: http://www.7activestudio.com info@7activestudio.com http://www.7activemedical.com/ info@7activemedical.com http://www.sciencetuts.com/ 7activestudio@gmail.com Contact: +91- 9700061777, +91- 9100061777 7 Active Technology Solutions Pvt.Ltd. is an educational 3D digital content provider for K-12. We also customise the content as per your requirement for companies platform providers colleges etc . 7 Active driving force "The Joy of Happy Learning" -- is what makes difference from other digital content providers. We consider Student needs, Lecturer needs and College needs in designing the 3D & 2D Animated Video Lectures. We are carrying a huge 3D Digital Library ready to use. MANUFACURE OF PORTLAND CEMENT:Raw Materials: The raw materials required for cement manufacture are. Lime stone which provides calcium. Clay which provides aluminium and silica.Cement is manufactured by two methods they are. Wet process. Dry process. Now let us discuss wet process and dry process detailed.WET PROCESS:In the wet process, first the clay is purified by washing in a wash mill.The lime stone is crushed into small particles and mixed with purified clay in proper proportions to get raw slurry.DRY PROCESS: In the dry process the raw materials are mixed in proper proportions.The mixture is dried, pulverized (Crushed into fine particles) and made uniform. The resulting powder is called "raw material".The raw slurry or raw meal, obtained by one of wet or dry process called charge. Charge is introduced into a rotary Kiln.The rotary kiln consists of a steel cylinder about 150meters long and 4meter diameter and rotates 30 to 60 turns per hour.At one end of the cylinder a screw conveyer is arranged which slowly allows the charge into the cylinder.The other end of the cylinder, a burneris arranged coal or burning oil is burnt at this end.The charge entering the cylinder slowly moves towards the hot end.At the burning end of the kiln, the temperature is around 1700 to 1900degrees centigrade, at this end some chemical reactions takes place between calcium oxide and aluminium silicates.Mixture of calcium silicates and calcium aluminates is formed.The resultant product consists of gray hard balls called clinker cement.Clinker cement is cooled, ground to fine powder and mixed with 2 to 3 percent of gypsum.
Đăng nhận xét